University of Twente Secures €950,000 for Advanced Metal 3D Printing Research
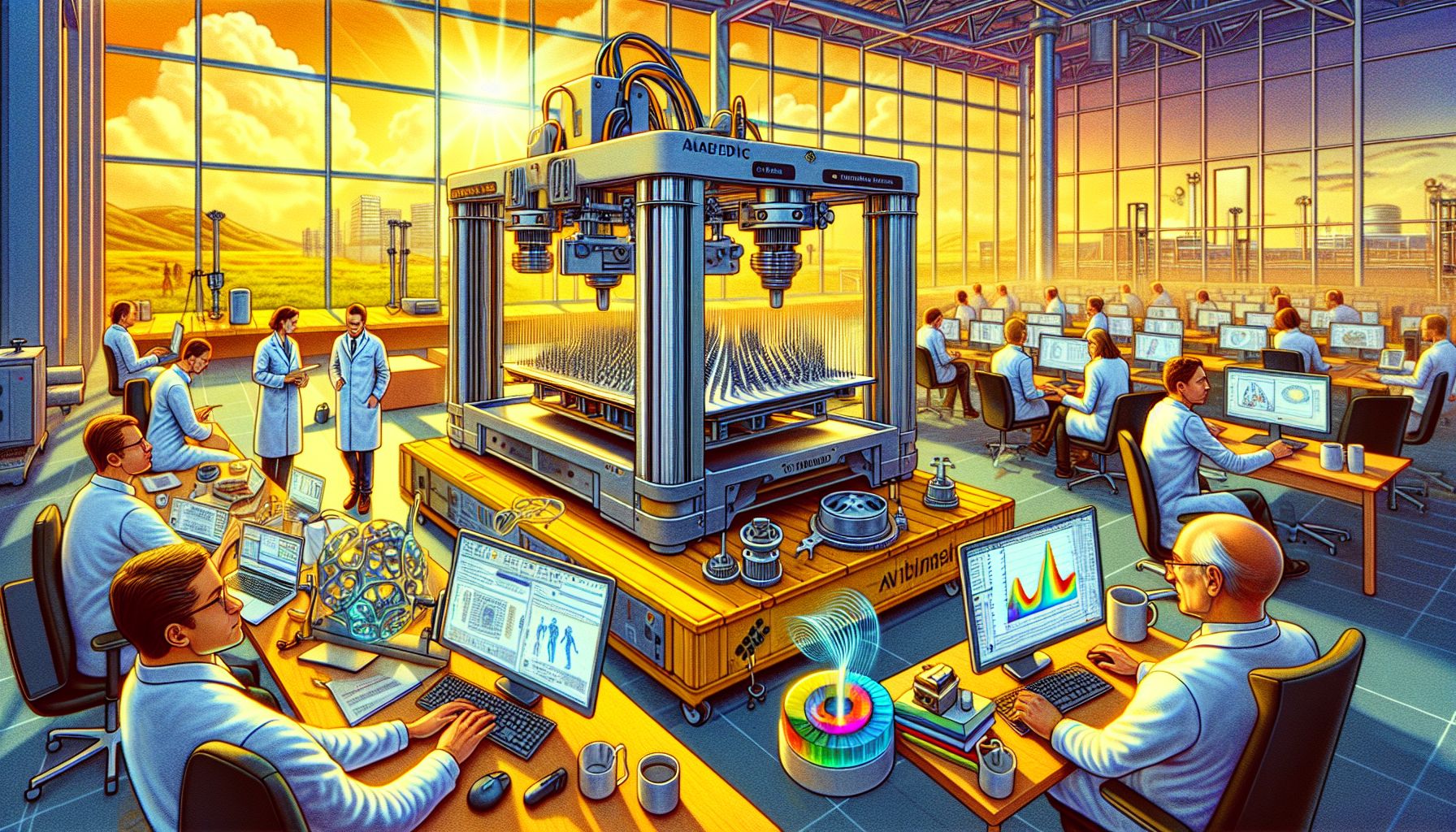
Enschede, Wednesday, 24 July 2024.
Researchers at the University of Twente have been awarded a €950,000 grant to enhance the safe use of metals in 3D printing. The project aims to develop an innovative vibration-based Non-Destructive Testing methodology, integrating data-driven models and explainable AI for autonomous inspection of metal 3D-printed parts.
A Leap in 3D Printing Safety
The initiative, led by Dr. Liangliang Cheng from the Engineering and Technology Institute Groningen, focuses on addressing one of the critical challenges in additive manufacturing (AM) — ensuring the quality and safety of 3D-printed metal parts. This project is particularly significant given the growing reliance on 3D printing technology across various industries, from aerospace to medical devices.
Collaboration and Funding
This groundbreaking research is a collaborative effort between the University of Twente, the University of Groningen, and the Technical University of Delft. The funding comes from the NWO Open Technology Programme, with industrial partners contributing over €100,000. The collaboration aims to leverage the expertise of these institutions to develop a robust and industrially applicable solution for the inspection and qualification of metal AM components.
The Role of Vibration-Based Non-Destructive Testing
Key to this research is the development of an advanced vibration-based Non-Destructive Testing (NDT) methodology. This technique involves using vibrations to detect flaws within metal parts without causing any damage. By integrating data-driven models and explainable AI, the project aims to create a system capable of autonomously inspecting and qualifying metal parts during the manufacturing process. This approach promises to significantly enhance the reliability and safety of 3D-printed metal components.
Implications for the Future
The successful implementation of this technology could revolutionize the way industries approach the quality assurance of 3D-printed metal parts. By enabling real-time, autonomous inspections, manufacturers can ensure higher standards of safety and reliability, thereby expanding the applications of 3D-printed metals in critical fields such as aerospace, automotive, and healthcare. This project not only represents a significant advancement in 3D printing technology but also underscores the importance of interdisciplinary collaboration in driving technological innovation.