Innovative Robot Revolutionizes Wind Turbine Maintenance
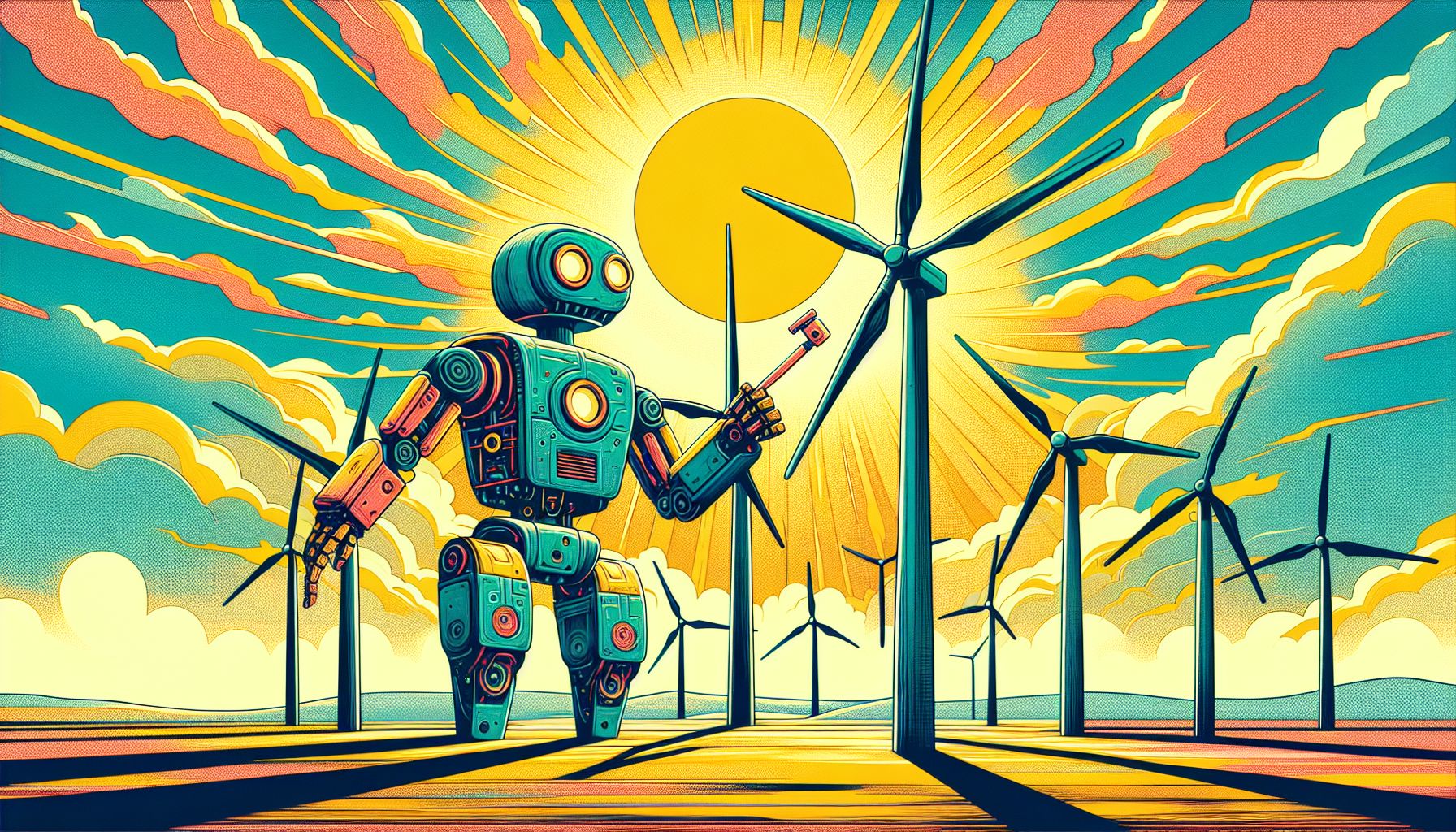
Delft, Thursday, 10 April 2025.
A new robot developed by TNO, TU Delft, and Robohouse autonomously installs sensors inside wind turbine blades, aiming to improve maintenance and operational efficiency.
Revolutionary Sensor Installation Technology
The innovative robot, developed in The Hague-based TNO’s laboratories [1], represents a significant advancement in wind turbine maintenance technology. The system autonomously installs sensors deep within wind turbine blades, reaching areas that were previously inaccessible to human technicians [2]. The first working prototype demonstrated its capabilities in early 2025 during testing on a 32-meter Vestas V66 wind turbine blade at the Zephyros Field Lab [3].
Advanced Features and Capabilities
The robot’s sophisticated design incorporates multiple automated functions essential for precise sensor installation. According to Wim Castricum, an engineer at TNO, ‘Using robots, we can install sensors deeper within the blade and collect real-time data on its condition and structural integrity, without an engineer having to crawl inside the blade’ [3]. The system includes automated positioning, surface preparation capabilities, and precision sensor placement mechanisms [3]. A high-resolution camera enables real-time monitoring and control, allowing a single technician to manage the entire installation process from the turbine’s base [4].
Future Implementation and Impact
The project is currently transitioning to its next crucial phase, which involves validation in real wind turbine environments with industry partners [3]. Project manager Janaki Mohanan Nair at TNO indicates that future enhancements may include AI-driven navigation, cable attachment features, and integration with broader turbine monitoring systems [3]. This innovation emerges as part of TNO’s broader commitment to sustainable energy solutions, operating within their comprehensive research initiatives aimed at driving the transition to net-zero emissions [5].