Teijin Aramid Innovates with AI for Delfzijl Factory Maintenance
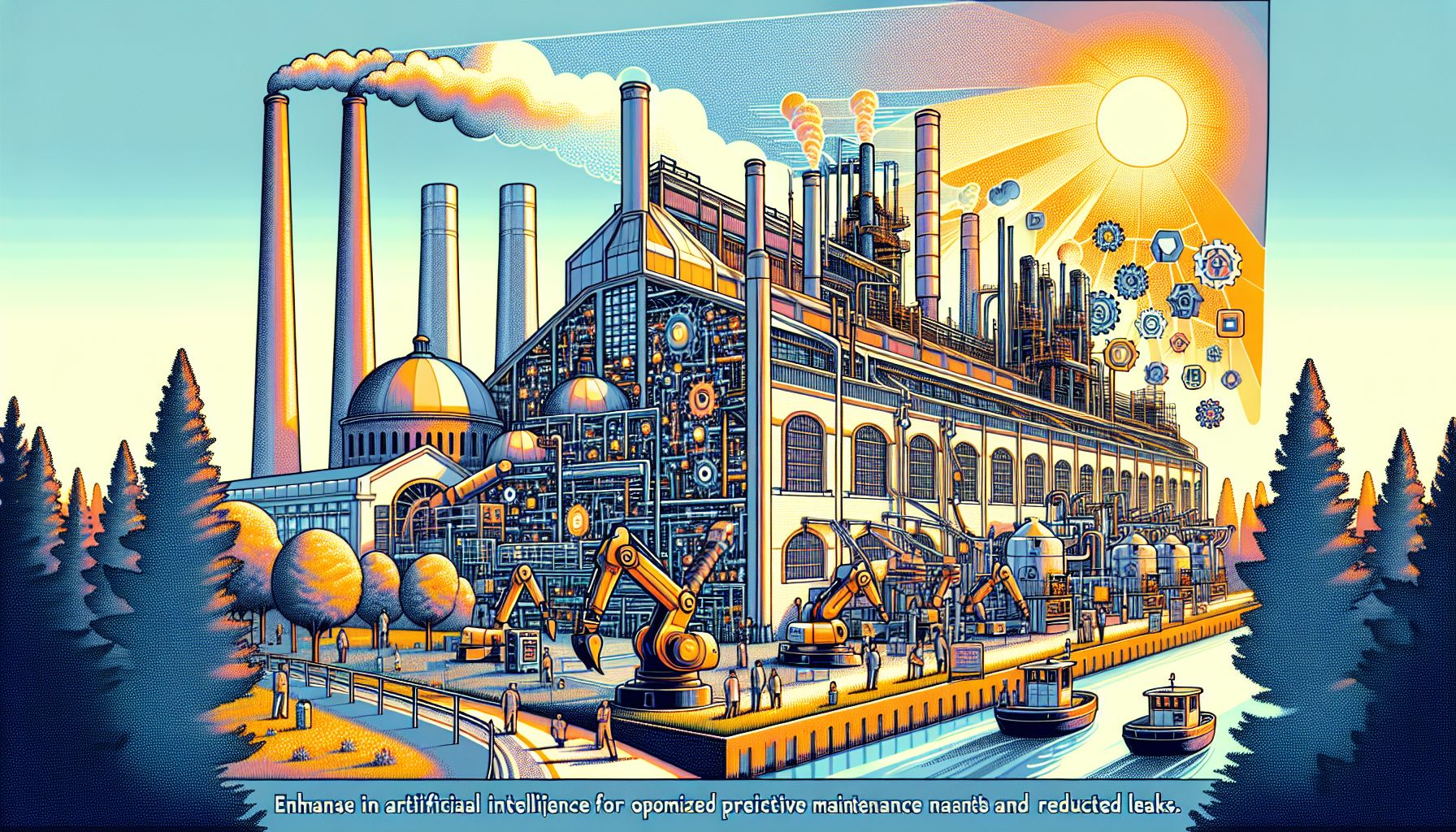
Delfzijl, Friday, 17 January 2025.
Teijin Aramid launches a pioneering AI project in the Netherlands to optimize predictive maintenance and reduce leaks, aiming for enhanced efficiency during a major maintenance stop.
Strategic Implementation of AI Technology
Teijin Aramid is set to commence its most extensive maintenance shutdown at their Delfzijl chemical plant in April 2025 [1][2]. The twelve-week operation will feature an innovative pilot program implementing data analysis and artificial intelligence for predictive maintenance [1]. Site manager Nina Huck explains that while traditional methods involve regular inspections of pipes and connections, this new approach utilizes AI to proactively identify potential weak points before issues arise [3].
Advanced Data Analysis System
The predictive maintenance system leverages existing inspection data stored in SAP, partnering with industry leaders like Stork and IBM to analyze patterns through machine learning [1]. The system specifically targets the thousands of pipes and connections throughout the facility, aiming to prevent leaks before they occur [1]. The effectiveness of the AI predictions will be validated during the maintenance shutdown, with inspectors checking identified weak points for issues such as corrosion [3].
Safety and Environmental Benefits
While the facility reported no major leaks in the previous year, the implementation of AI-driven maintenance represents a significant step toward enhancing both safety and environmental protection [1]. The technology aims to minimize unexpected leaks that could potentially endanger workers and contractors on site [1]. If successful, the pilot program will be expanded, with plans to involve regulatory authorities in the innovation process [1].
Economic Impact and Future Prospects
The introduction of AI-powered maintenance is expected to deliver substantial economic benefits through more targeted maintenance procedures [1]. This approach could potentially reduce the frequency of inspections and unexpected leaks, resulting in significant cost savings [1]. The success of this pilot program in the coming months will be crucial in determining its broader implementation across the chemical industry, potentially setting a new standard for maintenance procedures in Northern Netherlands and beyond [1].