First Multi-Story 3D-Printed Homes to Begin Construction in 2025
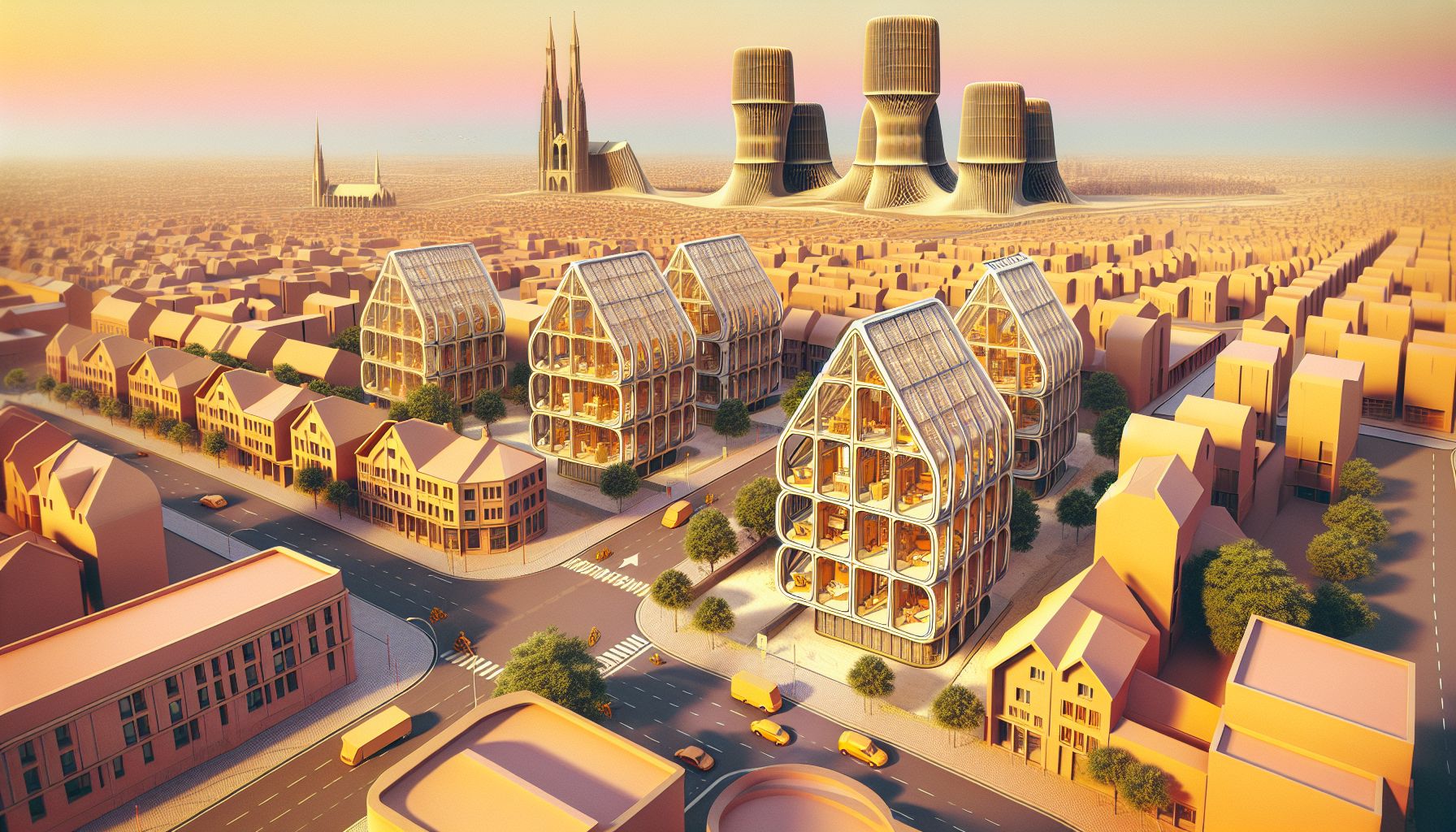
In early 2025, construction will start on four new 3D-printed owner-occupied homes in Eindhoven’s Bosrijk neighborhood, showcasing significant advancements in construction technology.
Innovative Construction Technology
The upcoming construction of multi-story 3D-printed homes in Eindhoven’s Bosrijk neighborhood marks a groundbreaking advancement in the housing sector. This innovative project, part of Project Milestone, aims to revolutionize the way homes are built, focusing on efficiency, sustainability, and customization.
Benefits of 3D Printing in Construction
One of the primary benefits of 3D printing in construction is the significant reduction in construction time and cost. Traditional building methods are often labor-intensive and time-consuming, but 3D printing can produce a house in a fraction of the time. For example, industrial-sized 3D printers have been reported to complete the printing of an entire house in less than 24 hours, excluding additional construction time for on-site assembly[1]. This rapid production capability translates to lower labor costs and faster project completion times.
How 3D Printing Technology Works
The process of 3D printing houses involves creating structures layer by layer using a specialized printer. These printers use a variety of materials including cement blends, sand, polymers, and bio-resins[2]. In the case of the Bosrijk homes, the facade will be printed separately from the inner and outer walls, which includes insulation to enhance circularity and make parts easier to reuse[3]. This method not only reduces waste but also allows for a high degree of customization in design.
Key Players and Their Roles
The construction of these homes is a collaborative effort involving several key players. The Municipality of Eindhoven, Eindhoven University of Technology (TU/e), and companies like Saint-Gobain Weber Beamix, Van Wijnen, Houben/Van Mierlo Architects, and Witteveen+Bos are all part of the Project Milestone initiative[4]. Professor Theo Salet from TU/e leads the research on concrete printing, focusing on digitizing the construction process to achieve time and cost savings while enhancing sustainability and industrial customization[3].
Scaling Up for Wider Adoption
Professor Salet emphasizes the importance of scaling up the technology to make it widely available and to fully exploit its advantages. According to him, the current focus is on aligning the concrete, printer, and design within the construction team to ensure the successful scaling up of this innovative technology[3]. The collaboration among partners is crucial in achieving consistent quality and efficiency in printing multiple homes simultaneously.
The Future of 3D-Printed Homes
The success of the Bosrijk project could pave the way for broader adoption of 3D-printed homes around the world. With the potential to address housing shortages, reduce construction waste, and lower costs, 3D printing technology holds promise for the future of sustainable construction. As Professor Salet noted, continuous development and scaling up of this technology will be key to realizing its full potential and making these benefits accessible on a larger scale[4].